BMW’s AI Now Guides Humans Through Quality Control Checks
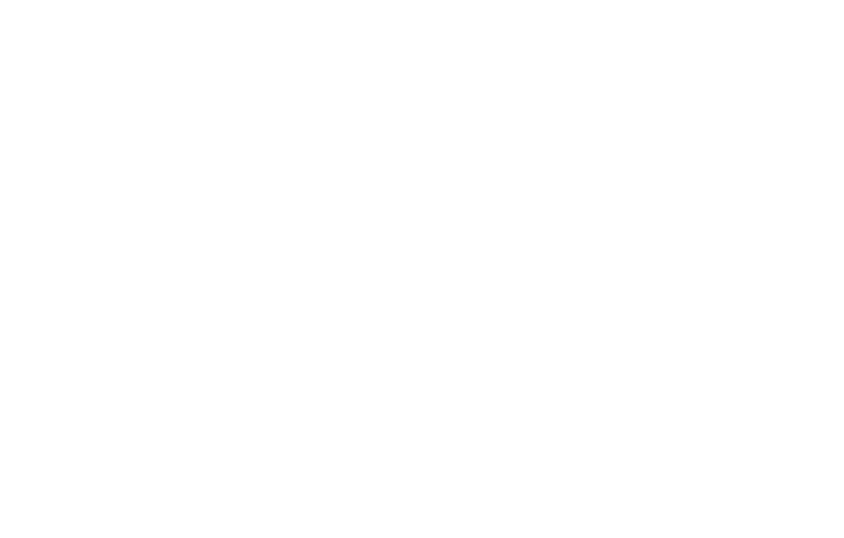
Published: May 7th, 2025.
At BMW’s Regensburg plant, artificial intelligence isn’t building your next car — it’s telling humans how to check if it was constructed correctly.
As part of a pilot project called GenAI4Q, BMW has developed a machine learning system that generates customized quality inspection plans for every vehicle rolling off the line — roughly 1,400 cars per day, one every 57 seconds. That includes gas, hybrid, and fully electric cars, each built to individual customer specs.
However, AI is not inspecting the cars. Instead, it acts like a data-driven quality strategist. It analyzes each vehicle’s unique features, production status, and recent trends, then tells human workers what to inspect and in what order — all delivered via a sleek smartphone app that includes voice input and real-time checklists.
On the surface, this is a clear win for precision and efficiency. Traditional one-size-fits-all quality control checklists may overlook edge cases, such as a quirky feature or a package that is rarely selected but warrants extra scrutiny, due to the multitude of variants on one line. Based on live data and past patterns, BMW’s AI determines which elements deserve attention.
According to Armin Ebner, head of the Regensburg plant, it’s part of BMW’s push toward a “digitally connected factory.” And for customers, the upside is easy to grasp: fewer defects, faster fixes, and fewer recalls.
Suppose your plug-in X1 has a specific driver assistance module that recently caused issues. The AI, recognizing a trend, might flag that feature for closer inspection. In theory, your car gets more intelligent quality control, tailored to its needs.
Here’s where things get more complicated.
BMW is essentially letting AI decide what counts as “worth checking” on a vehicle, and that decision is only as good as the system’s training data. What if a part starts failing, but the data doesn’t show it clearly yet? What if a correlation is mistaken for a cause? A sharp-eyed tech might catch something outside the checklist in a human system. Will AI-trained routines encourage too much trust in the software’s decisions?
It is also worth noting that while the current system augments human inspection, it's easy to imagine a future phase where AI isn’t just advising—it’s also replacing. That's a slippery slope familiar to anyone watching automation in manufacturing. BMW says the system makes workers’ jobs easier, not obsolete, for now.
Unlike the flashy generative tools used to write stories or generate images, GenAI4Q uses the same underlying principles for something much more grounded: generating logic and workflow for physical production. It’s operational AI and will likely come to more industries soon.
The system was co-developed with Munich startup Datagon AI, and it represents one of the clearest examples of real-world generative AI doing more than chat — it’s helping make strategic decisions in manufacturing.
BMW’s AI-driven inspection pilot feels like a meaningful step forward, but also raises challenging questions. Are we redefining quality through algorithms? Will future cars be designed based on the easiest to inspect, not the best to drive? Will workers slowly lose the discretion and judgment that make them quality humans?
What is clear is that AI isn’t just driving the future of mobility — it’s increasingly shaping the invisible processes behind the scenes. Whether that leads to smarter cars or just smarter shortcuts will depend on how carefully companies like BMW balance innovation with oversight.